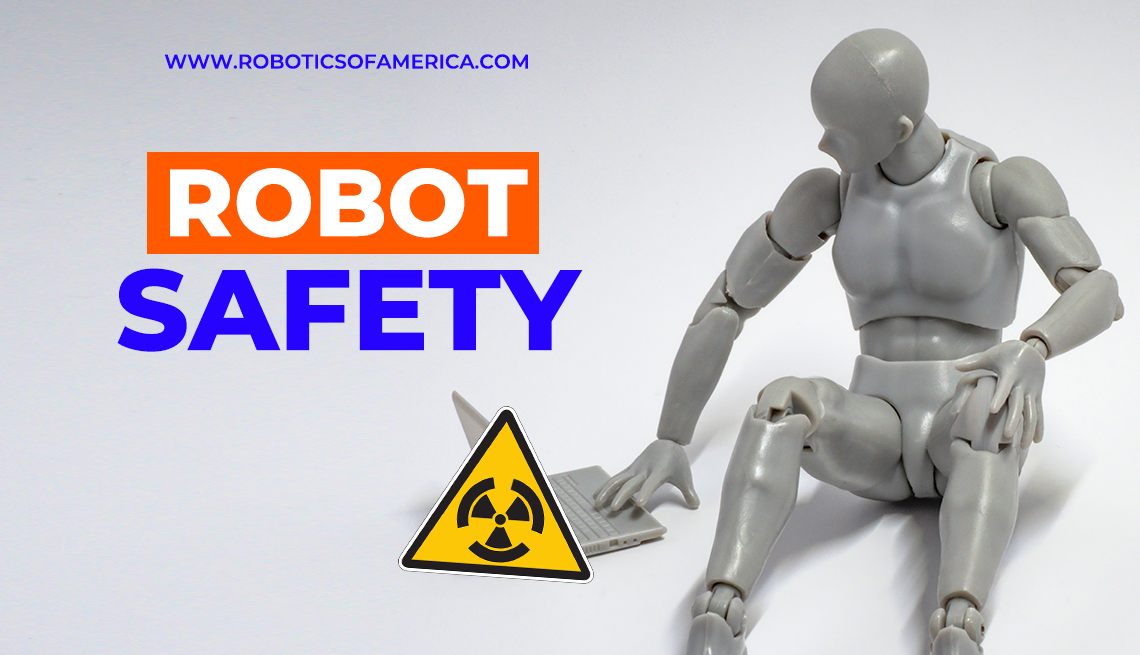
The Importance of Robot Safety
Robot Safety
Robot safety has never mattered more than right now. Why? Because industrial robots are becoming more advanced by the day. Their popularity among the business community is impressive. But with that popularity comes concerns about the safety of workers. In order for humans and robots to work together, proper guidelines must be in place.
There’s no way around it. Robots are sometimes dangerous to use for a variety of tasks. That danger only increases when a company does not have safety protocols in place. Many organizations make one huge mistake. They assume that the standards for operation are good enough to maintain safety.
They are not. Any company needs a set of specific robot safety standards. These are the standards that ensure robotic operations will not be dangerous. Robots have not been on this earth for very long. Because of this, robotic safety standards are always changing. Better yet, they are evolving. Let’s examine some popular issues associated with the concept of robot safety.
Are There Already Standards for Robot Safety?
Yes, robot safety standards already exist. So, what is a robot safety standard? it is a series of specific guidelines about a robot’s operations. The guidelines focus on procedures and specifications that keep humans safe. Anyone who constructs, sells, or uses robots must follow the guidelines. But keep the following notion in mind. (This is where it gets confusing.) There are different robot guidelines in place depending on what type of robot you use. Why? Because different robotics industry groups have created their own sets of standards.
So, which set of robot safety guidelines should your company refer to? It depends on the model of a robot that you're using. When in doubt, it’s best to contact the manufacturer of your robot. Listed below are the most common robot safety guideline organizations. It is likely that your company should follow the standards of one of these groups:
- -The US Standards Body. (This can include any of the following groups. JISC. CSA. AFNOR. BSI. DIN.)
- -ANSI. (The American National Standards Institute)
- -IEC. (The International Electrotechnical Commission)
- -ISO. (The International Organization for Standardization)
- -The International Standards Body
Again, adhering to one of these robot safety groups should benefit your organization. Each group will provide you with expert-level safety advice related to your robots. Safety groups like these are making a difference. They are helping to ensure that accidents and fatalities do not take place.
Why Do Robot Safety Standards Matter?
There are many obvious factors for why robot safety is so important. For one, safety standards ensure that the robotics industry will continue to grow. That is why thousands of experts across the globe are making efforts to boost safety. The findings of these experts lead to new safety standards getting put in place.
Keep in mind that each country has unique robot safety guidelines. But do not let this notion confuse you. There are international safety organizations doing their best to address common concerns. In fact, robot safety standards are now more cohesive than they were a decade ago.
This has led to industrial robots having way more uses than in previous decades. What’s the end result? Tons of sales for industrial robots. In fact, this is one of the reasons why robotic safety standards matter so much. Industrial robots are benefiting thousands of companies around the world. This means that more humans are near robots than at any other point in history.
Robot safety guidelines will continue to change in the coming years. That’s because the global market for robots, itself, is experiencing many changes. What is the most important takeaway from current robot safety standards? It is that companies must train their workers about all relevant safety protocols. This needs to take place whenever a company purchases a new robot.
Training should occur even if the new robots are the updated versions of a company’s previous bots. As long as companies commit to robot stay training, most accidents should get avoided. Otherwise, businesses will risk having their workers get maimed or die. This will lead to government intervention and lawsuits.
Robot Safety Guidelines Have Evolved Over the Years
There was never much chaos across worksites when robot safety was a brand-new issue. Why? Workers were always advised to keep a safe distance from their robotic co-workers. This is for good reason. The use of industrial robots carries many potential hazards. What is the main reason for this?
Still to this day, many robots lack needed sensory abilities. In other words, keep the following notion in mind. Industrial robots are continuing to struggle to detect when humans are close-by.
1984 was when many organizations realized how important robot safety is. That’s because a die-cast operator passed away while working. The operator became trapped between a steel pole and hydraulic industrial robot. The worker’s death led to NIOSH releasing a list of new robot safety tactics.
(NIOSH is The National Institute for Occupational Safety located in the United States.) Most of the tactics focused on one key factor. It was to have workers maintain a consistent distance between robots and themselves.
As the years have progressed, so too have the guidelines for robot safety. Factors such as physical barriers and robotic sensors are making a difference. These mechanisms have been protecting workers for decades. The average modern industrial robot can now shut down on its own when people are too close. Some experts speculate that certain robot safety standards will soon get relaxed.
Why? Because robots are so much “smarter” than they were in 1984. Their artificial intelligence capabilities have improved by a lot since then. This means that companies soon might not need to put up so many barriers.
As of now, most industrial robots have fences or cages placed around them. But do not assume that your company can go ahead and relax its standards. It is best to wait until an official robotics safety organization gives the green light. That’s why companies should keep up with relevant organizations. A great example is the American National Standards Institute. Are you unsure of which organization to turn to?
Do you need guidelines for your company’s models of robots? If so, contact Robotics of America right now. Our experts will connect you to the correct robotics safety organization. This will ensure that your team is following all the needed protocols.
The 4 Most Common Guarding Methods for Robot Safety
Robot safety should matter to you and your company. If it does, make sure that your team is aware of the following guarding methods. These are common measures to prevent industrial workers from getting injured.
1) The Robot Safety Interlocked Barrier Guard
This robot safety method involves placing a physical barrier around an industrial robot. It ensures that the work envelope gets protected. For example, the gate to the work envelope can feature interlocks. Interlocks ensure that operations will comes to a halt whenever a human approaches. Once a human leaves and the gate closes, a worker presses a control switch. Robotic operations then start up again. If you need help finding a quality interlocked fence, you can contact Robotics of America.
2) The Robot Safety Fixed Barrier Guard
This fixed barrier guard functions as a robot safety fence. It is so stable that special tools have to remove it. The concept of this barrier guard is like the interlocked barrier guard. Worker clearance is easy thanks to this guard’s advanced controlled conditions. Robots are able to reach parts with ease despite this guard’s full enclosure.
3) Robot Safety Awareness Barrier Devices
Safety perimeters matter when it comes to robot safety. And an awareness barrier device is a much-needed industrial perimeter. Suspended chains and low railings are common examples of awareness barrier devices. These devices prevent works from accessing a robot’s work envelope. But workers can still climb over the devices in case there is an emergency. This should only take place when a supervisor states that a potential hazard risk is minimal. Otherwise, an awareness barrier device can help. It prevents people from getting too close to robotic systems hazards.
4) Presence Sensing Robot Safety Devices
Robot safety has improved across the board thanks to presence sensing instruments. Examples of these devices include light curtains and pressure mats. A pressure-sensitive mat is an example of a device that detects movement. Once again, this prevents workers from stepping too close to industrial robots. Other common presence sensing detectors include:
- -lasers
- -proximity detectors
- -radio frequencies
- -electrical capacitance
Conclusion: Robot Safety Guidelines Prevent Accidents From Taking Place
Your team should review robot safety guidelines on a consistent basis. The guidelines will prevent your workers from suffering injuries. But the key to great prevention is worker training. Your company should have a full-scale robotic safety training program in place. This is so each employee will know how to interact with your robots in a safe, secure manner. If you have questions about robot safety, please contact Robotics of America today. Our experts will help you find the best guidelines that fit your operations. Also, feel free to browse our site for more robot safety content. We are releasing many more articles on topics such as:
- -robot safety systems
- -industrial robot safety
- -robot safety standards
- -robotics safety rules
- -robot safety checklist
- -robot safety training
- -OSHA robot safety
- -robot safety PDF